پيداوار جي متحرڪ دنيا ۾، ڪارڪردگي ۽ درستگي تمام ضروري آهي. صنعتون مسلسل اهڙيون ٽيڪنالاجيون ڳولينديون آهن جيڪي معيار جي اعليٰ معيار کي برقرار رکندي پيداوار کي وڌائين.اسپاٽ ويلڊرزڌاتو جي حصن کي موثر ۽ قابل اعتماد طريقي سان ڳنڍڻ لاءِ مختلف صنعتن ۾ اهم اوزار آهن. اچو ته ڪجهه ڪيسن ۾ ڏسون ته جيئنمختلف صنعتن کي ڪيئن فائدو ٿيو آهيجديد اسپاٽ ويلڊنگ مشينن جي استعمال کان.
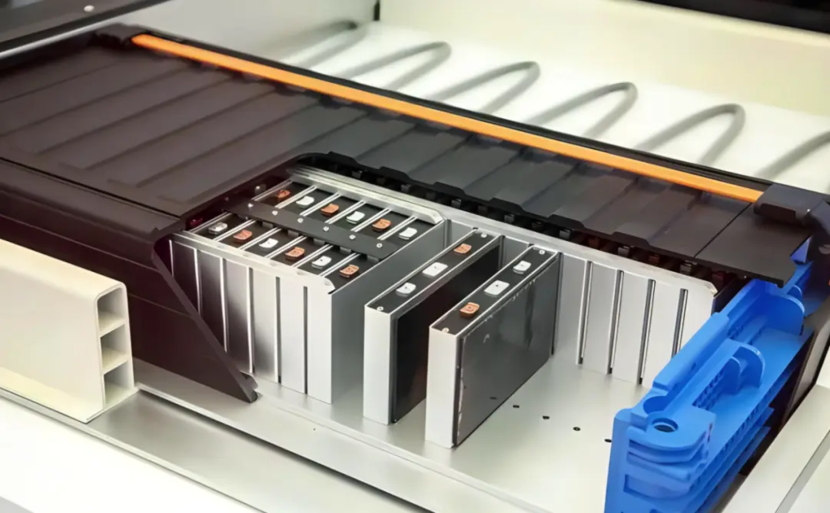
گاڏين جي صنعت: پيداوار ۽ حفاظت کي وڌائڻ
جديد اسپاٽ ويلڊنگ مشينن مان سڀ کان اهم فائدو حاصل ڪندڙ آٽوميٽو انڊسٽري آهي. ٽيسلا ۽ بي ايم ڊبليو جهڙن ڪار ٺاهيندڙن انهن مشينن کي پنهنجي پيداواري لائينن ۾ ضم ڪيو آهي، جنهن جي نتيجي ۾ رفتار ۽ درستگي ٻنهي ۾ قابل ذڪر بهتري آئي آهي.
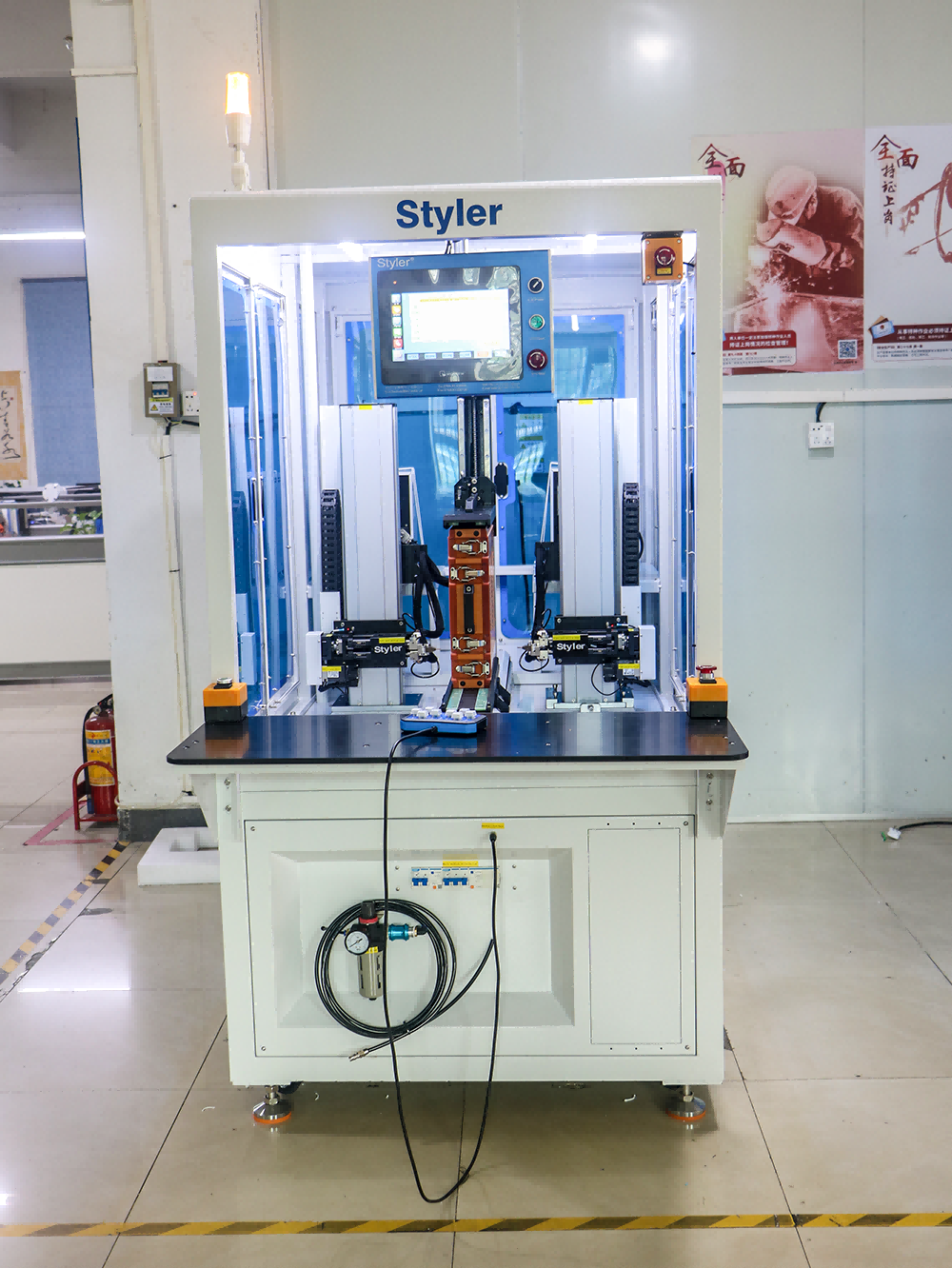
مثال: ٽيسلا
ٽيسلا جي گيگا فيڪٽري پنهنجي برقي گاڏين کي گڏ ڪرڻ لاءِ بيٽري ويلڊ ڪرڻ لاءِ جديد ترين اسپاٽ ويلڊنگ مشينون استعمال ڪري ٿي. اهي مشينون مسلسل ويلڊ معيار کي يقيني بڻائين ٿيون، جيڪو ڪارن جي ساخت جي سالميت لاءِ اهم آهي. اهو نه رڳو ڪار جي حفاظت کي بهتر بڻائي ٿو، پر پيداوار جي ڪارڪردگي کي به بهتر بڻائي ٿو.
اليڪٽرانڪس جي پيداوار: درستگي ۽ اعتبار
اليڪٽرانڪس جي شعبي ۾، اليڪٽرانڪس انڊسٽري جديد اسپاٽ ويلڊنگ مشينن کي اپنائڻ ذريعي اهم ترقي ڪئي آهي. اهي مشينون بي عيب ۽ قابل اعتماد ڪنيڪشن سان اليڪٽرانڪ ڊوائيسز جي پيداوار کي آسان بڻائين ٿيون، سرڪٽ ۽ جزو جي سالميت کي يقيني بڻائين ٿيون. نتيجي طور، ٺاهيندڙ پيداوار جي عملن کي منظم ڪندي اعليٰ معيار جي اليڪٽرانڪس جي وڌندڙ گهرج کي پورو ڪرڻ جي قابل آهن.
مثال: HUAWEI
HUAWEI جون پيداواري سهولتون پنهنجي ڊوائيسز کي گڏ ڪرڻ لاءِ جديد اسپاٽ ويلڊنگ مشينن جو استعمال ڪن ٿيون. اهي مشينون HUAWEI جي نازڪ حصن کي سنڀالڻ لاءِ گهربل درستگي فراهم ڪن ٿيون. نتيجو خرابين ۾ هڪ اهم گهٽتائي ۽ پيداوار جي ڪارڪردگي ۾ اضافو آهي، جنهن جي ڪري HUAWEI معيار تي سمجهوتو ڪرڻ کان سواءِ اعليٰ صارفين جي گهرج کي پورو ڪري سگهي ٿو.
ايرو اسپيس انڊسٽري: سخت معيارن کي پورو ڪرڻ
ايرو اسپيس انڊسٽري پڻ جديد اسپاٽ ويلڊنگ مشينن جا فائدا حاصل ڪري رهي آهي. اهي مشينون ايرو اسپيس ٺاهيندڙن کي پيچيده حصن کي اعليٰ ترين درستگي سان ويلڊ ڪرڻ جي قابل بڻائين ٿيون، جهاز جي پيداوار لاءِ گهربل سخت معيار جي معيارن کي پورو ڪندي.
مثال: بوئنگ
بوئنگ پنهنجي جهاز جي تياري ۾ جديد اسپاٽ ويلڊنگ ٽيڪنالاجي کي شامل ڪيو آهي. انهن مشينن جي درستگي ۽ اعتبار يقيني بڻائي ٿو ته هر ويلڊ ايرو اسپيس انجنيئرنگ ۾ گهربل سخت حفاظتي معيارن کي پورو ڪري ٿو. هن اپنائڻ سان نه رڳو جهاز جي ساخت جي سالميت بهتر ٿي آهي پر پيداوار جو وقت به گهٽجي ويو آهي، جنهن سان بوئنگ کي ترسيل شيڊول کي وڌيڪ اثرائتي طريقي سان پورو ڪرڻ جي اجازت ملي آهي.
ان کان علاوه، ڌاتو جي ٺاھڻ ۽ تعمير ۾، ترقي يافته اسپاٽ ويلڊر صنعتن کي مضبوط ۽ پائيدار ڍانچو ٺاهڻ جي قابل بڻائين ٿا. اهو ڌاتو پينلن کي گڏ ڪري سگھي ٿو، اهي مشينون لچڪدار انفراسٽرڪچر ۽ عمارت جي عنصرن کي تعمير ڪرڻ لاءِ ويلڊنگ آپريشن جي ڪارڪردگي ۽ درستگي کي وڌائين ٿيون.
انهن متنوع صنعتن ۾ اهي مثال ترقي يافته اسپاٽ ويلڊنگ مشينن جي تبديلي واري اثر کي ظاهر ڪن ٿا. آٽوميٽو ۽ اليڪٽرانڪس جي پيداوار ۾ پيداوار جي رفتار ۽ درستگي کي وڌائڻ کان وٺي ايرو اسپيس ۽ ڌاتو جي بناوت ۾ سخت حفاظتي معيارن کي پورو ڪرڻ تائين، مهيا ڪيل ڪيس اسٽڊيز اهو ظاهر ڪن ٿا ته اهي مشينون ڪيئن پيداوار جي معيار کي بلند ڪري رهيون آهن، صنعتن کي انهن جي شعبن ۾ معيار، ڪارڪردگي ۽ جدت ۾ شانداريت حاصل ڪرڻ جي قابل بڻائي رهيون آهن. جيئن ٽيڪنالاجي اڳتي وڌندي رهي ٿي، اسپاٽ ويلڊنگ مشينن ۾ وڌيڪ واڌارن جي صلاحيت مستقبل ۾ وڌيڪ صنعتي فائدا آڻيندي.
At اسٽائلر، اسان بيٽري ٺاهيندڙن جي مخصوص ضرورتن مطابق جديد اسپاٽ ويلڊنگ سامان جي ڊيزائن ۽ تيار ڪرڻ ۾ ماهر آهيون. اسان جون جديد مشينون جديد ترين موجوده ڪنٽرول ٽيڪنالاجي کي شامل ڪن ٿيون، مختلف بيٽري ايپليڪيشنن لاءِ صحيح ۽ مسلسل ويلڊز کي يقيني بڻائين ٿيون. ڇا توهان صارف اليڪٽرانڪس لاءِ ليٿيم آئن بيٽريون ٺاهي رهيا آهيو يا اعليٰ ڪارڪردگي واري برقي گاڏين لاءِ، اسان جا جديد اسپاٽ ويلڊنگ حل توهان کي توهان جي پيداوار ۾ اعليٰ معيار، اعتبار ۽ حفاظت حاصل ڪرڻ جي طاقت ڏين ٿا.
عمل.
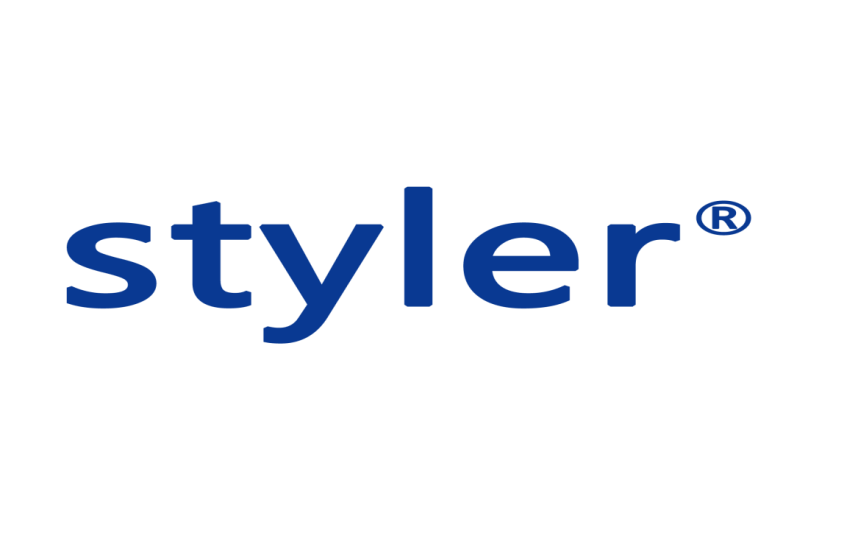
پوسٽ جو وقت: جولاءِ-31-2024